Product overview
Multi-arc ion coating machine is a newly developed vacuum ion coating technology in recent years. The ion coating technology using arc discharge principle under vacuum state is the first vacuum coating method developed. It has the advantages of high deposition rate, firm bonding, stable equipment operation, etc. On the basis of the traditional multi-arc, our company has made strict improvements and designs on the target sealing structure, magnets, cooling, etc., which has increased the ionization rate, refined the particles, and the film layer and the substrate are firmly bonded, and the film layer is more dense. Improved hardness and wear resistance, suitable for plating decorative films such as golden titanium nitride, black titanium carbide, colorful titanium oxynitride, etc., and can also be coated with anticorrosive touch film (such as AL, Cr stainless steel and TIN, etc.) and wear resistance Membrane. The film layer is firmly combined with the substrate, which is suitable for watches, hardware, tableware, and tools and molds that require wear resistance and superhardness. It has good development prospects.
Technical parameter
Device model |
VLT-800 type |
VLT-1000 type |
VLT-1200 type |
Coating room size |
800×1250 |
1000×1200 |
1200×1500 |
Ultimate vacuum |
≤4×10-4pa |
Pump down time |
从大气抽至6.6×10-2Pa<10min |
Arc source |
6 (2KW/piece) |
8 (2KW/piece) |
6 (2KW/piece) |
DC negative bias |
0-1000V 10A
0-500 20A |
0-1000V 12A
0-500 25A |
0-1000V 20A
0-500 30A |
Workpiece size |
6 axis (220×800) |
6 axis (250×1000) |
6 axis (280×1300) |
Heating power |
15KW |
20KW |
25KW |
Total power/average power |
40KW/25KW |
50KW/30KW |
58KW/35KW |
Magnetron target (planar or cylindrical target) |
10KW |
15KW |
20KW |
Gas mass flow controller |
Three way |
Three way |
Three way |
Equipment characteristics
Production period: the production period is short -270sec/1 the same period (conditions for dry products without a large amount of outgassing)
Coating material: universally used for various metal coatings (aluminum, nickel, copper, chromium... and other metal materials)
Coating method: metal sputtering coating, uniform film thickness distribution
Coating quality: high brightness, strong adhesion
Coating speed: two 20Kw high-power magnetically controlled sputtering motors, the power can be adjusted to control the coating speed
Dehumidification capacity: The vacuum chamber is equipped with a low temperature refrigeration system below 140 degrees, which fully absorbs moisture to increase the vacuum reach speed
Operating expenses: The sputtering electrode is a self-developed product, which greatly improves the use efficiency of the target material
Occupy the ground finely: loading and unloading at a fixed position requires only a small operating space
Operation method: The man-machine interface can be set and monitored intuitively, and the person who has no management password can not change it
After-sales service: There is an after-sales service center and parts warehouse, which can quickly deal with problems in use
Equipment principle diagram
In a suitable vacuum environment, connect the high-voltage power supply to establish a low-pressure gas discharge low-temperature plasma zone between the evaporation source and the substrate. The substrate electrode is connected to a DC negative high voltage to form a glow discharge cathode, and the plating material vaporizes atoms. Entering this area collides with inert gas ions and electrons, and the ionized ions and gas ions bombard the surface of the coating with higher energy, depositing the evaporate or its reactants on the laminate.
Schematic diagram of ion plating
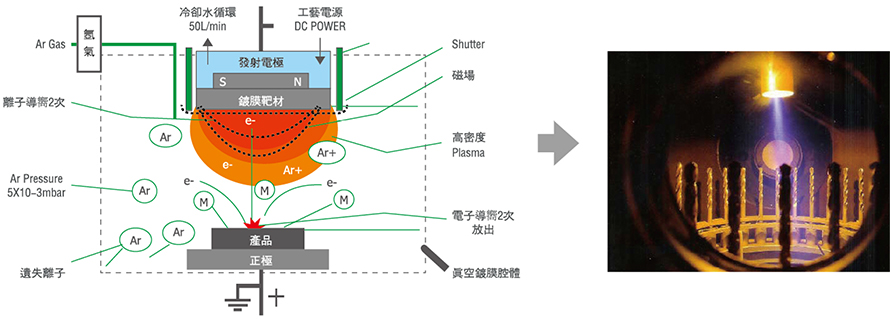